在工业生产的众多环节中,板材厚度测量的重要性不言而喻。无论是建筑领域的钢梁结构、汽车制造的车身板材,还是电子设备的外壳,板材的厚度都直接关乎产品质量与性能。哪怕是微小的厚度偏差,都可能引发严重的安全隐患或使用问题。
传统的板材厚度测量方法,如卡尺测量、超声波测量等,各有弊端。卡尺测量效率低、易受人为因素干扰;超声波测量则在精度和稳定性上有所欠缺,面对高精度需求时常力不从心。
而激光位移传感器的出现,为板材厚度测量带来了革命性的变化。它宛如一位精准的 “测量大师”,凭借先进的激光技术,实现非接触式测量,不仅精度极高,还能快速、稳定地获取数据,有效规避了传统测量方式的诸多问题。接下来,让我们一同深入探究,两台激光位移传感器是如何默契配合,精准测量板材片材厚度的。
激光位移传感器测厚原理大揭秘
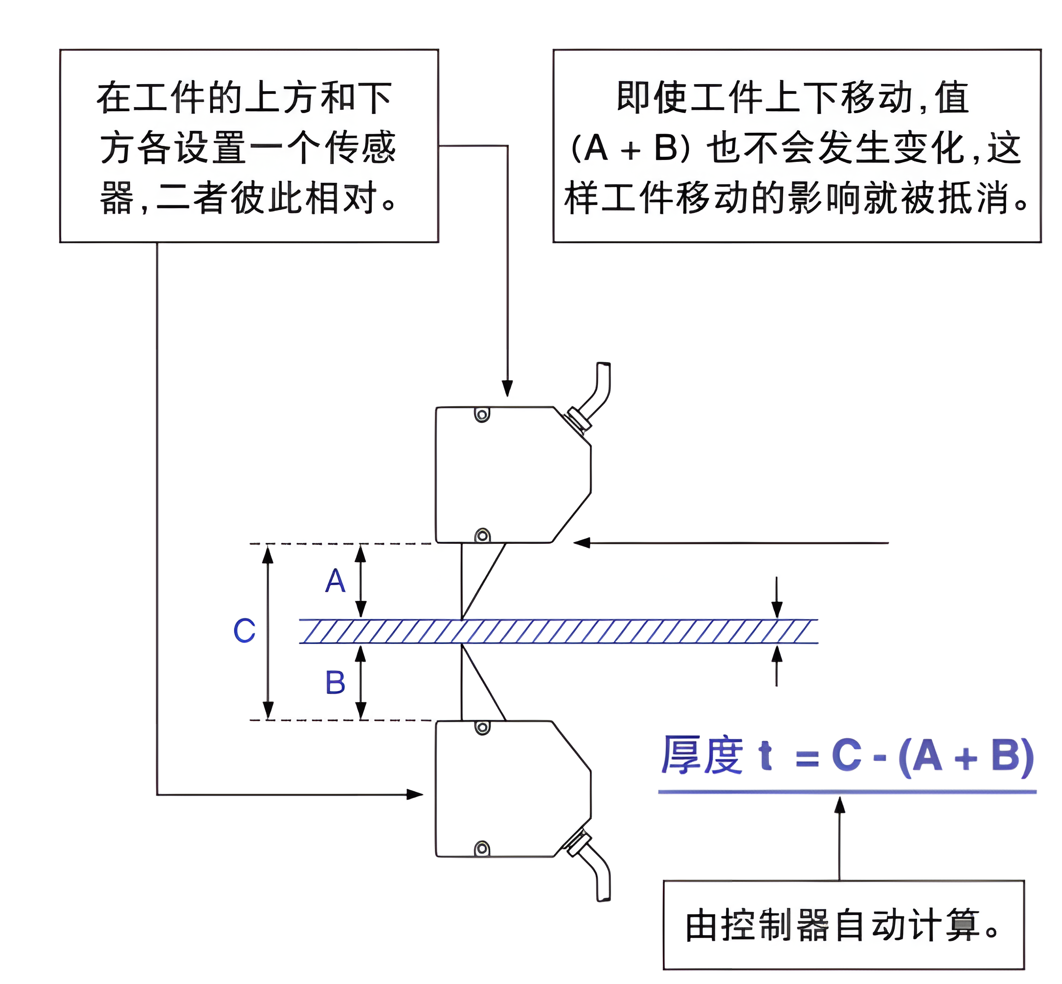
当谈及利用两台激光位移传感器对射安装测量板材片材厚度的原理,其实并不复杂。想象一下,在板材的上下方各精准安置一台激光位移传感器,它们如同两位目光犀利的 “卫士”,紧紧 “盯” 着板材。
上方的传感器发射出一道激光束,这束激光垂直射向板材的上表面,而后经板材上表面反射回来。传感器凭借内部精密的光学系统与信号处理单元,迅速捕捉反射光的信息,并通过复杂而精准的算法,计算出传感器到板材上表面的距离,我们暂且将这个距离记为 。
与此同时,下方的传感器也在同步运作。它发射的激光束射向板材的下表面,同样经过反射、捕捉与计算,得出传感器到板材下表面的距离 。而这两台传感器在安装之初,它们之间的垂直距离 便已精确测定。
如此一来,板材的厚度 便呼之欲出,依据简单而精妙的公式 即可算出。为了让大家更直观地理解,特意附上一张清晰明了的示意图(此处可插入或描述类似参考资料中的厚度差分测量原理示意图)。通过这张图,相信大家能一眼看穿其中的奥秘,对测量原理有更为透彻的领悟。
测厚系统的精心设计
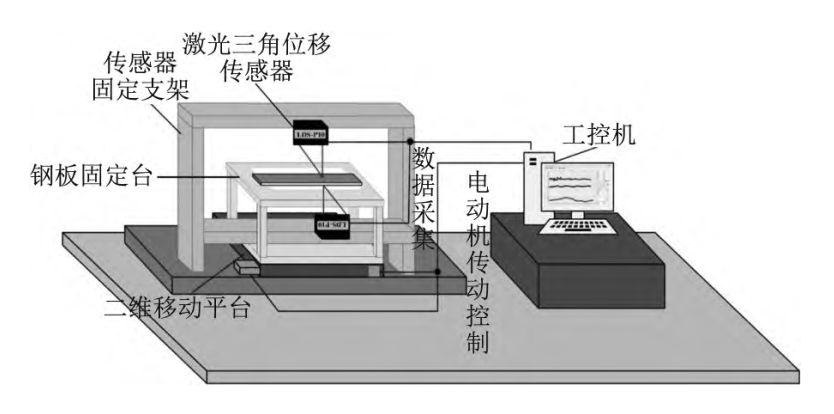
(一)测量装置的巧妙构造
这套用于板材厚度测量的系统,其测量装置的设计独具匠心。基座作为整个装置的 “根基”,采用高稳定性材料精心打造,内部巧妙安置隔振措施,宛如一位沉稳的 “大力士”,稳稳地支撑起整个测量装置,同时将外部振动无情地隔绝在外,为精准测量营造出稳定的环境。传感器支架呈稳定的 “A” 字型龙门式结构,恰似两座坚固的 “瞭望塔”,精准地固定上下两个超精密激光位移传感器,确保它们始终保持差动布局,实现对样板厚度的同步、精准测量。样板固定台采用中空框架式一体结构,如同一只温柔而有力的 “大手”,可靠地固定被测样板,保证样板在测量过程中稳如泰山,厚度测量稳定可靠。移动平台则依托二维精密导轨,如同为样板固定台装上了 “风火轮”,能精准控制其在 、 两个方向平稳移动、可靠定位,轻松实现多点位的厚度测量,全方位捕捉样板厚度信息。
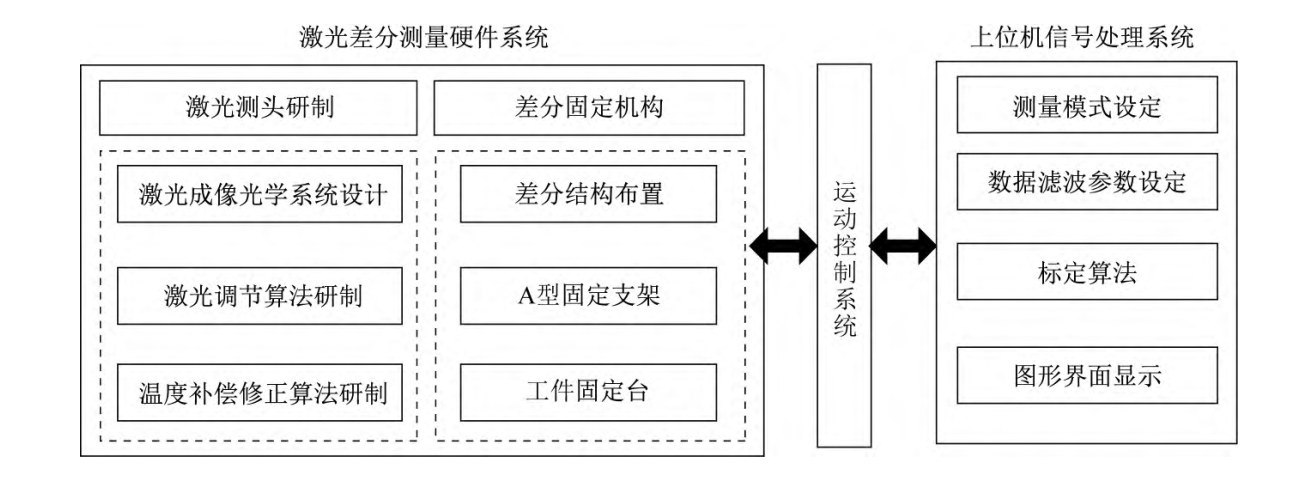
(二)主控系统的关键构成
主控系统同样是整个测量系统的 “智慧大脑”,由差分测量系统、运动控制系统和信号处理系统等几大 “核心成员” 组成。差分测量系统宛如一位专注的 “数据收集者”,负责同步采集上下两个激光位移传感器的数据,并迅速将这些数据传送至计算机进行深度处理,通过精密的差分算法,精准还原出板材的厚度信息。运动控制系统则像一位精准的 “指挥官”,控制和驱动测量装置中的电动机,使被测样板在 、 两个方向精确移动,实现测点的快速、准确定位,确保测量无死角。信号处理系统如同一位精明的 “分析师”,承担着数据的采集、计算处理及标定和补偿等关键算法工作,运用先进的滤波算法去除数据噪声,通过巧妙的标定和补偿算法修正系统误差,最后将处理后的数据和直观的图形展示出来,为操作人员提供清晰、准确的测量结果。这三大系统紧密协作,共同推动测量工作高效、精准地进行。
硬件构成:精准测量的基石
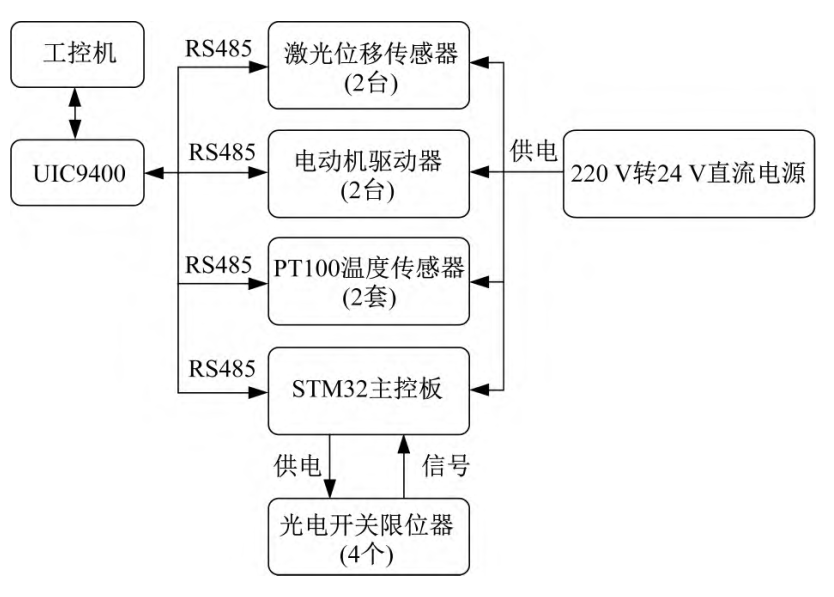
(一)激光位移传感器的严苛选型
在整个测量系统中,激光位移传感器无疑是最为关键的 “主角” 之一,其选型的精准度直接关乎测量成败。光源的抉择堪称重中之重,经过反复权衡与大量实验验证,波长处于 400 - 650nm 范围的激光二极管脱颖而出。这一区间的光源,稳定性表现卓越,能在复杂多变的工业环境中 “稳如泰山”,为测量提供可靠的基础;同时,在成本控制上也达到了理想的平衡,兼顾了企业的投入产出效益。然而,激光二极管发射的光线天生带有一定发散角,难以直接满足高精度测量对光线准直性的严苛要求。为攻克这一难题,高性能的准直镜组 “闪亮登场”。它宛如一位神奇的 “光线魔法师”,能够巧妙地将发散的光线梳理成近乎完美的平行光束,确保激光精准无误地射向目标板材,大大提升了测量的准确性。不仅如此,聚焦镜组的聚焦光斑尺寸也被精心调控,务必使其控制在微米级。如此精细的光斑,能够在板材表面精准 “定位”,捕捉到最为细微的高度变化,不放过任何一个影响测量精度的细节。在滤光片的设计上,同样倾注了大量心血。石英滤光片凭借其优异的光学性能和耐高温特性,毫无争议地成为首选。其带宽被严格限定在不超过 50nm 的范围内,这一精细的设置有效屏蔽了杂散光的干扰,确保测量系统能够以极高的灵敏度精准感知板材表面的反射光信息,为厚度测量的高精度提供了坚实保障。通过对这些关键部件的精心挑选与优化组合,激光位移传感器的性能得以全方位提升,为板材厚度测量的高精度、高稳定性筑牢了根基。
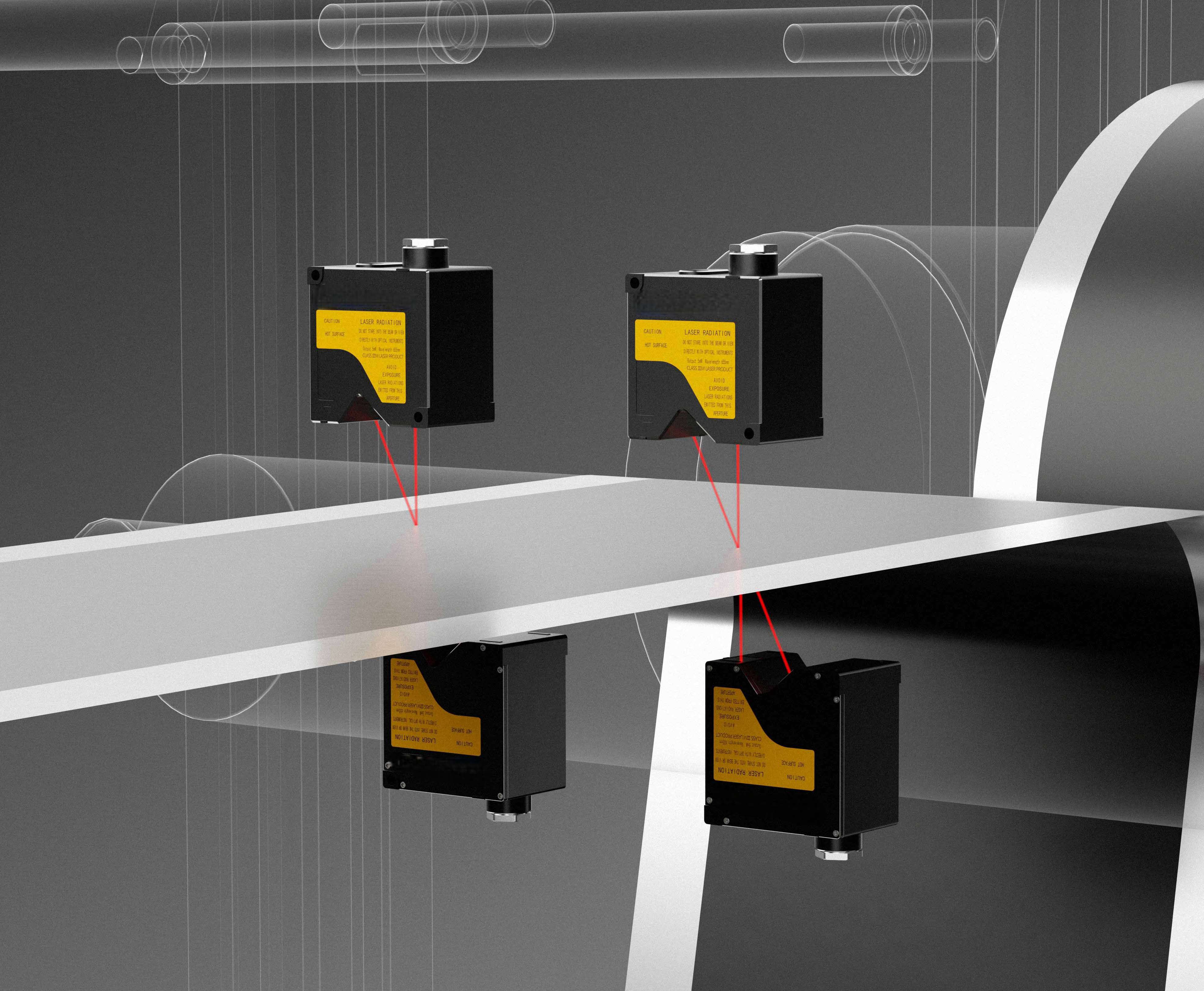
(二)STM32 系列处理器的高效掌控
STM32 系列处理器在整个测量系统中扮演着 “智慧中枢” 的关键角色,肩负着底层逻辑控制的重任,是确保系统高效、精准运行的核心力量。在电动机脉冲驱动方面,它展现出卓越的掌控能力。通过向电动机精准、快速地发送脉冲信号,如同一位经验丰富的 “车夫” 熟练驾驭马车一般,驱动二维移动平台平稳、高效地运行。这使得被测样板能够在 、 两个方向上迅速而精准地移动,快速定位到各个测量点,大大提高了测量效率。同时,在测量系统零位控制上,STM32 处理器同样表现出色。它能够以极高的精度确定测量系统的初始零位,为后续测量数据的准确性提供了可靠的基准。每次测量启动时,处理器都会迅速校准零位,确保测量数据如同从 “原点” 出发,精准无误。而且,该处理器与工控机之间建立了紧密、高效的联通机制,二者协同作战,信号转化模块更是锦上添花。它如同一位出色的 “翻译官”,轻松实现不同信号的输入和输出转换,将各种复杂的信号汇总至上位机进行统一通信控制。这一过程不仅高效流畅,还为系统后续的功能扩展和升级预留了充足的空间,使得整个系统能够紧跟科技发展的步伐,不断适应日益复杂的测量需求。
(三)UIC9400 多路串口通信模块的无缝连接
UIC9400 多路串口通信模块在整个测量系统中犹如一条条无形的 “信息高速路”,搭建起了各部件之间无缝通信的桥梁,是保障系统协调运行的关键枢纽。它的核心使命是实现不同信号的输入和输出转换,确保各种信号在系统中能够顺畅无阻地流通。在实际运行中,它一端紧密连接着 2 台温度变送器、2 台激光位移传感器以及 2 台电动机驱动器,另一端与 STM32 处理器精准对接,如同一位严谨的 “交通指挥官”,有条不紊地汇总、调度着各方信号。而导轨上的限位光电开关则如同系统的 “安全卫士”,直接与 STM32 处理器相连,实时监控着样板的位置信息,一旦样板趋近边界,便立即向处理器发出警报,确保测量过程安全无虞。通过 UIC9400 模块的高效运作,整个系统实现了信息的实时共享与协同处理,各部件之间紧密配合,宛如一支训练有素的交响乐团,共同奏响了精准测量的华丽乐章。
软件实现:智能测厚的 “大脑”
(一)运动控制及测量模块的精准调度
运动控制及测量模块宛如一位严谨的 “调度大师”,掌控着整个测量流程的节奏与精准度。它精心设定了导轨的运动模式以及传感器在每个测量点的采集方式,为操作人员提供了手动和自动两种便捷的测量模式。
在手动测量模式下,操作人员可根据实际需求,灵活选择单点测量或 81 点测量。当进行 81 点测量时,一场精密的 “点位舞蹈” 便在 2mm×2mm 的区域内精彩上演。测量装置中的电动机在该模块的精准驱动下,带动被测样板在 、 两个方向稳步移动,如同一位优雅的舞者在舞台上精准走位,实现 81 个测量点的精确定位。传感器则如同敏锐的 “观察者”,在每个点上迅速采集数据,不放过任何细微的厚度变化,随后这些宝贵的数据被有条不紊地记录下来,为后续的分析处理提供坚实基础。
自动测量模式更是将高效与精准展现得淋漓尽致。只需简单设置,系统便能自动按照预设程序,快速、精准地完成对样板各个点位的测量。这一过程不仅大大节省了人力,还确保了测量的一致性和准确性,为大规模、高效率的生产提供了有力支持。
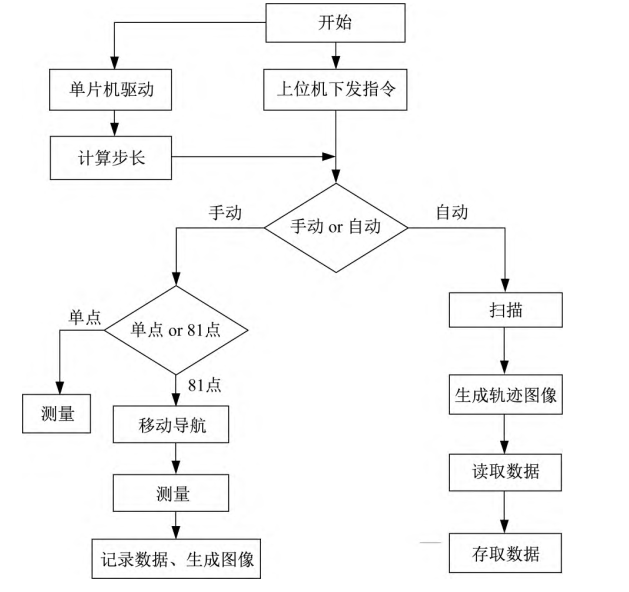
(二)测量数据滤波模块的精细优化
测量数据滤波模块无疑是一位 “数据净化大师”,致力于为测量结果的准确性保驾护航。在测量过程中,由于环境噪声、设备微小振动等诸多因素的干扰,传感器采集到的数据难免会混入一些 “杂质”,影响最终测量的精度。
为了去除这些 “杂质”,该模块巧妙运用中值滤波和平滑滤波相结合的方法,对传感器的测量数据及计算得到的钢板厚度值进行深度 “清洗”。首先登场的中值滤波,犹如一位智慧的 “筛子”,能够精准识别并去除粗差。它在众多数据中挑选出最具代表性的中值,有效排除那些因突发干扰而产生的异常值,确保数据的稳定性。接着,平滑滤波器如同一位细腻的 “画师”,对经过中值滤波的数据进行进一步润色。它通过巧妙的算法,减小相邻测量值之间的偏差,让数据曲线更加平滑、连续,真实反映板材的厚度变化趋势。通过这两步精细的滤波操作,测量的重复性得到了极大优化,数据的准确性和可靠性大幅提升,为后续的决策判断提供了坚实依据。
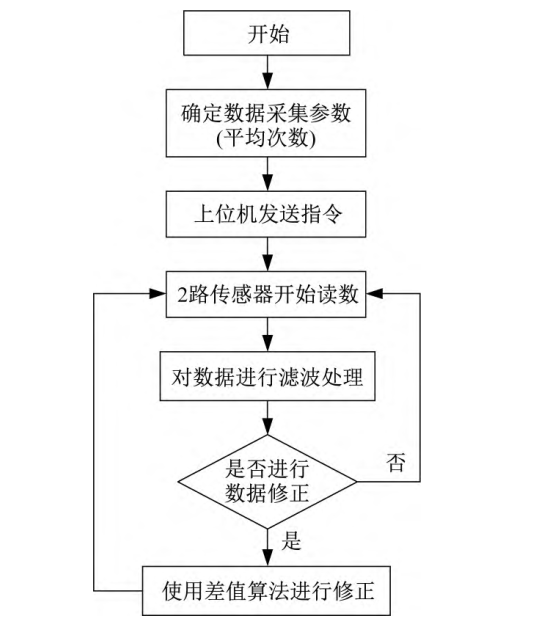
(三)图像显示模块的直观呈现
图像显示界面模块恰似一位出色的 “视觉翻译官”,将复杂的数据转化为直观、易懂的图像和信息,让操作人员能够一目了然地掌握测量情况。它精心打造的界面涵盖了多个关键画面,每个画面都有着独特的功能。
状态显示与运动控制画面如同系统的 “仪表盘”,实时呈现测量系统的当前状态,包括传感器的工作状态、导轨的位置、测量进度等关键信息。操作人员只需轻轻一瞥,便能对整个测量流程心中有数,及时发现并解决潜在问题。
通信与校准画面则是系统的 “通讯中枢”,清晰展示系统与各设备之间的通信连接状态,确保数据传输的稳定与顺畅。同时,它还为操作人员提供了便捷的校准操作入口,方便定期对系统进行校准,保证测量的准确性。
手动扫描画面和轨迹扫描画面如同测量过程的 “实时记录仪”,以动态的形式展示测量点的分布以及测量轨迹,让操作人员直观了解测量的覆盖范围和路径,确保无遗漏、无偏差。
扩展功能画面更是为系统的未来发展预留了无限可能,随着技术的不断进步,新的功能插件可以轻松融入其中,进一步拓展系统的应用场景和深度分析能力,满足日益复杂的工业需求。
实战测试:用数据说话
(一)重复性测试:稳定可靠的见证
重复性测试是衡量测量系统稳定性的关键指标。我们精心挑选了不同规格的标准陶瓷量块,涵盖了从 0.5mm 到 4.0mm 的多种厚度,对其中心点展开了细致入微的重复性测试。在测试过程中,针对测量点附近 2mm×2mm 的微小区域,进行了多次微动扫描。每完成一次扫描,便精准记录下一个测试结果,随后将 、 两个方向的导轨归零,待装置稳定后,再次重复上述操作,如此往复多次。经过严谨的计算,得出 10 次测试结果之间的标准差。从测试数据来看,当厚度为 0.5mm 时,测量结果的重复性可达 0.10μm;厚度为 1.0mm 时,重复性为 0.16μm;2.0mm 厚度对应的重复性是 0.24μm;3.0mm 厚度下重复性为 0.16μm;4.0mm 厚度时重复性为 0.17μm。这些数据充分表明,系统在面对不同厚度的板材时,均能保持极高的测量稳定性,重复性精度完全满足高标准的指标要求,为工业生产中的精准测量提供了坚实保障。
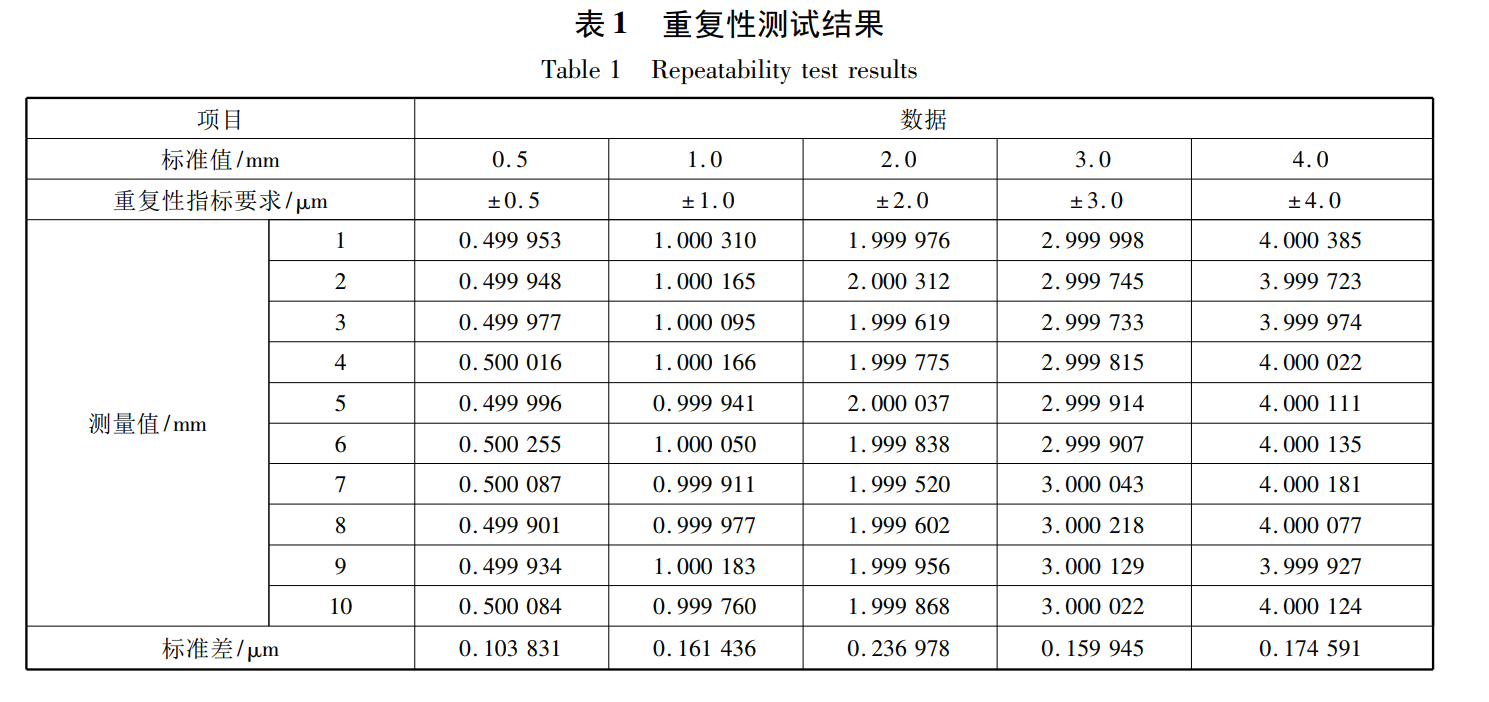
(二)测量允许误差:高精度的彰显
测量允许误差直接反映了系统的精度水准。此次测试,我们选用了 8 块精心校准的量块,其厚度从 0.5mm 到 4.0mm 不等,分布均匀,极具代表性。每块量块在样板盘所处位置的中心点都经过精确标记,以坐标点形式清晰呈现,确保测量的精准定位。执行自动标定程序时,采用先进的 3 次样条曲线法,依次对所有量块进行精细标定。标定完成后,对标准量块展开全面测量,测量范围覆盖 2mm×2mm 的矩形区域,确保获取的数据全面且准确。从测量结果来看,绝大多数厚度测量误差被精准控制在允许误差的 30% 以下,这意味着系统的测量精度远超预期,能够为高精度需求的工业生产提供可靠的数据支持,有力保障产品质量。
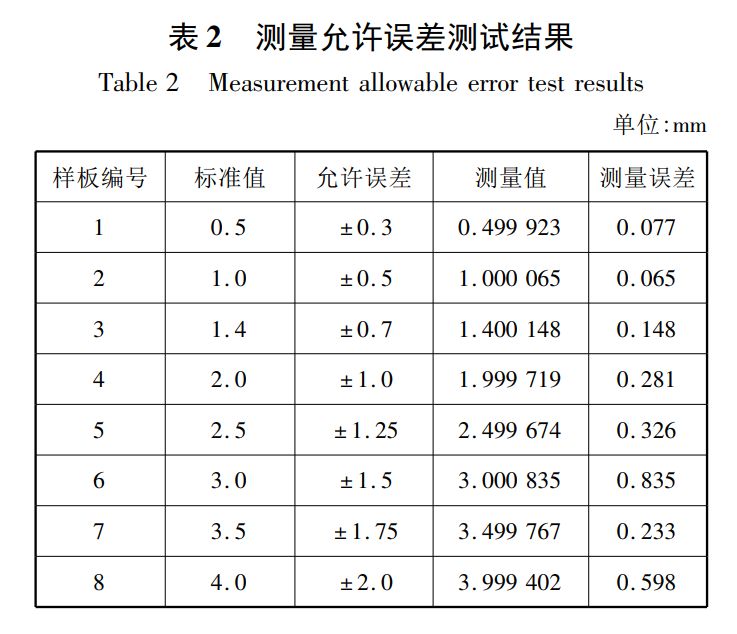
(三)测量漂移性:长期稳定的保障
测量漂移性测试则聚焦于系统在长时间测量过程中的可靠性。我们特意挑选了 4 种不同规格的标准量块,厚度分别为 0.5mm、1.5mm、2.5mm 和 4.0mm,模拟实际生产中可能遇到的各种厚度场景。在长达 10 小时的测试周期内,始终保持激光精准打在量块的同一个测量点上,连续不间断地进行测量,测量间隔精确控制在 1 秒,每组数据测量约 36000 点,全方位捕捉测量数据的细微变化。通过严谨计算每组测量数据的极大值、极小值、极差以及标准差,得出的结果令人振奋。对于这 4 种不同厚度的量块,其长期测量漂移性均优于 ±0.1%,完美契合指标要求。这充分证明,即使在长时间、高强度的测量任务下,系统依然能够稳定运行,确保测量数据的准确性始终如一,为工业生产中的连续监测提供了可靠保障。
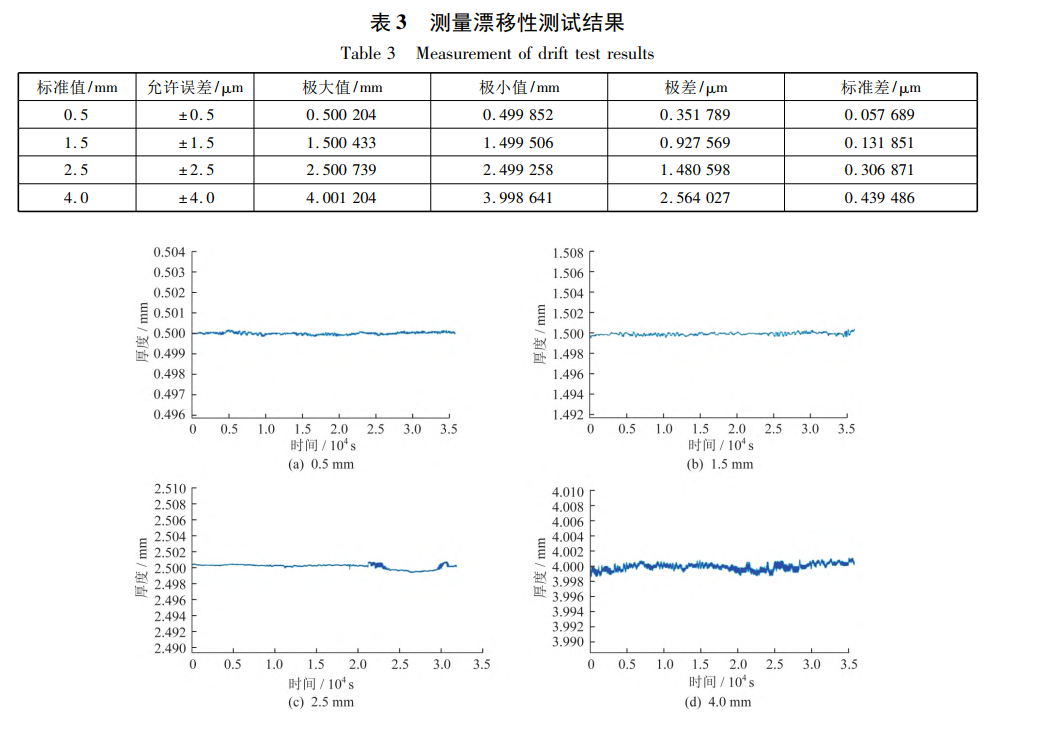
激光测厚,开启板材测量新篇章
通过对基于两台激光位移传感器对射安装的板材厚度测量系统的深入探究,我们清晰地见证了其卓越性能。高精度、非接触、安全可靠等诸多优势集于一身,使其在工业领域的应用前景无比广阔。
在汽车制造领域,汽车车身的板材厚度对于整车的安全性与性能表现起着决定性作用。激光位移传感器能够对车身板材进行快速、精准测量,确保每一块板材都符合严苛的质量标准,为汽车的轻量化设计与安全性能提升提供坚实保障,助力汽车行业迈向更高质量发展阶段。
在电子设备生产中,精密的电路板、外壳等部件对厚度精度有着极高要求。激光测厚系统凭借其微米级的测量精度,能够及时发现板材厚度的细微偏差,有效避免因厚度问题导致的电子设备性能故障,为电子产品的高质量、高可靠性生产保驾护航。
在航空航天领域,材料的质量与性能关乎飞行安全。激光位移传感器可对航空板材进行无损、高精度测量,确保板材质量万无一失,为飞行器的制造与维护提供精准数据支持,助力航空航天事业向着更高目标腾飞。
展望未来,随着科技的持续进步,激光位移传感器在板材厚度测量领域必将发挥更大作用。相信在科研人员的不懈努力下,测量系统的精度、稳定性和智能化水平将不断提升,为工业生产注入更强大动力,推动各行各业蓬勃发展,创造更加辉煌的未来。
本文参考摘抄自基于激光位移传感器的厚度测量校准系统设计及应用
孙 进, 于子金
( 宝山钢铁股份有限公司设备部, 上海 200941)