具有复杂自由曲面的超精密光学越来越多地应用于航空、航天、生物、消费电子等领域。优异的轮廓精度和表面光洁度是自由曲面光学成像性能的重要保证,同时这也给制造带来了严峻的挑战,限制了其广泛的应用。砂轮的几何误差、安装误差、轮廓误差等重要误差源都会对加工表面的轮廓精度产生影响。利用在线测量的方法对轮廓线误差进行补偿是提高轮廓线精度的有效途径,另一方面自由曲面光学系统的测量在不能损伤被加工表面的同时,需要实现亚微米精度。
来自哈尔滨工业大学的Qingliang Zhao团队采用非接触和在线测量的方法对已加工表面轮廓线误差进行测量和评价,建立基于误差源与被测轮廓线误差对应关系的刀具误差模型,对自由曲面光学磨削轮廓线误差补偿开展研究。
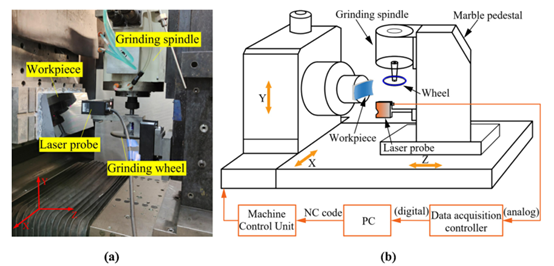
图1. 超精密磨床及在位测量系统:(a)系统实物图;(b)原理图。
如图1所示,在机测量系统安装在大理石底座上,靠近磨削主轴,使用激光位移传感器测量基底轮廓误差。补偿过程中的参数设置为进给速度为120 mm/min,采样频率为2 kHz。高精度激光位移传感器的测量数据需要滤除粗糙度等带来的中-高频率的空间信息,提取出有效的低频轮廓误差。
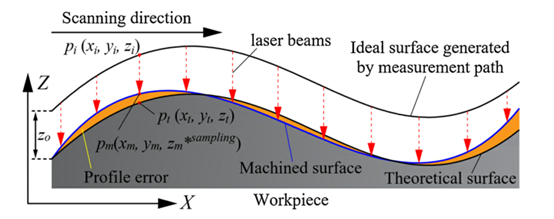
图2. 自由曲面轮廓误差示意图
轮廓误差的高精度测量和评定是自由曲面光学精密补偿加工的重要保证。自由曲面轮廓线误差一般以实际测量点与理想理论点之间的距离来计算。通过点扫描获取光学自由曲面的高精度低频轮廓误差信息。激光位移传感器测量的轮廓误差示意图如图2所示。通过工件目标几何参数生成的测量路径对磨削表面进行扫描。激光位移传感器的探头扫描工件表面,获得磨削表面的误差信息,由高精度数据采集控制器采集被测轮廓误差数据。然后对得到的数据进行重构,得到加工表面,并与理想理论表面进行比较,计算轮廓误差。
研究团队并通过小波分解技术,将用于补偿处理的低频轮廓误差从重构误差面中有效分离出来。最终实现沿工件长度(220 mm)和工件高度(105 mm)的轮廓误差分别从15.425 μm减小到1.678 μm和18.6 μm减小到1.6948 μm。在220m × 105mm测量范围内,经轮廓误差补偿后的加工面pv值由21.6 μm降至1.5486 μm。验证了所提轮廓误差补偿方法对双二次曲面的有效性。
论文标题:Ultra-precision raster grinding biconical opticswith a novel profile error compensation technique based on on-machinemeasurement and wavelet decomposition