为了提高自由曲面等元件的加工质量,需要对制造过程中产生的误差进行评估,以便及时发现偏差,从而反馈给后续加工工序。特别是在不从机床上卸载工件的情况下进行的在位测量(OMM),可以消除坐标损失带来的误差。近年来,采用激光位移传感器的激光三角测量OMM(LTOMM),是机械探头之外新发展起来的在位测量技术。
来自南京航空航天大学机电工程学院的DaweiDing等人提出了一种LTOMM误差模型和一种在设定精度约束下提高效率的路径规划方法。利用生成的路径,采用三坐标测量机(CMM)、OMM探头和LTOMM对自由曲面涡轮叶片进行检测,以评估各自的精度和效率。文章题为“Error Modeling and Path Planning for Freeform Surfaces by LaserTriangulation On-Machine Measurement”发表在“IEEETransactions on Instrumentation and Measurement”杂志。
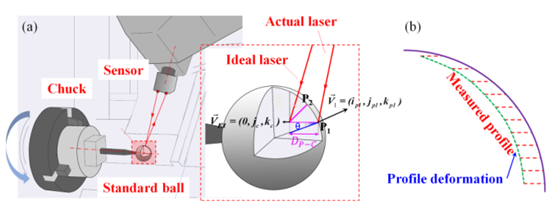
图1. 激光束校准误差。(a)误差校准原理图。(b)误差导致的标准球测量偏差。
误差方面,文章以Cook–Torrance(C-T) 照明模型,分析了倾角、位移和粗糙度的误差影响,并以标准球校准激光光束的指向性误差,如图1所示。在误差模型验证过程中,还考虑了温度、湿度、预热时间、被测表面颜色的影响。
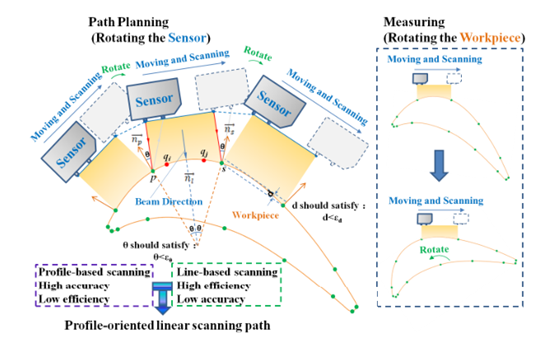
图2. 自由曲面测量角度和位移约束下的LTOMM路径规划。
路径规划方面。为了提高测量精度,需要对激光位移传感器进行详细的路径规划,通过调整入射角和扫描位移来满足要求。当测量精度给定时,可以计算出测量角度和位移的工作阈值。LTOMM的路径规划可以简单地描述为:1)分析总测量误差;2)将总误差划分到各个分量误差;3)计算测量的角度阈值和位移阈值;4)调整工件位置,直至角度平分线平行于激光束;5)将各个分段的规划路径进行连接。如图2所示。
规划的路径主要有直线型路径和轮廓型路径两种,它们的测量精度和效率各不相同。传感器在基于直线型路径上以特定的方向扫描,而在基于轮廓型路径上,它以不变的位移沿轮廓移动。基于直线路径的误差随着测量角度和位移的增大而增大;而基于轮廓路径的测量误差不受测量角度的影响,测量误差小于5 μm,在精度上具有优势。采用基于直线和基于轮廓的路径测量一个剖面所需时间分别为20 s和42 s。因此,两种路径的测量精度和效率不同,这将决定它们在生产线上的应用;粗扫描采用更有效的路径,而最终检测采用更精确的路径。
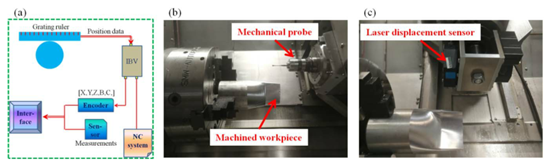
图3.用于加工工件轮廓测量的仪器配置。(a)自主研发的数据通信系统。(b) OMM采用机械探头。(c)采用激光三角位移传感器。
为了验证所提出的自由曲面测量方法,在车铣加工中心使用机械探头和激光位移传感器测量探头,使用如图3所示的配置。在实施在位测量之前,先对机械探头和激光位移传感器探头进行校准,并使激光位移传感器预热到稳定的温度。被测对象叶片型线先通过三坐标测量机进行测量,确定测量参考基准。随后,通过机械探针和激光位移传感器探头进行在位测量,测量值与三坐标的基准值进行对比进行性能评估。
沿着基于叶片轮廓线的路径,激光位移传感器探头测量的正负平均误差分别为+8.9和−9.9 μm,满足10 μm约束精度的前提。采用该路径完成测量所需时间为339 s,而采用内置机械探头所需的测量时间为1500 s。因此,采用激光位移传感器探头的测量时间显著减少了77.4%。
论文标题:Error Modeling and Path Planning for FreeformSurfaces by Laser Triangulation On-Machine Measurement