行业痛点与挑战
锂电池外壳边缘涂胶工艺(槽深5mm×宽3mm)对胶体连续性、填充均匀性及边缘贴合度要求严苛,直接影响电池密封性与安全性。传统激光位移传感器因光斑发散(≥50μm)、抗遮挡能力弱,在深窄槽内易受侧壁反射干扰,导致拐弯区域信号丢失、断胶漏检率高达15%以上。此外,胶体固化前的反光差异、产线振动及环境温漂(±5°C)进一步加剧测量误差,传统方案难以满足±10μm级在线检测需求。
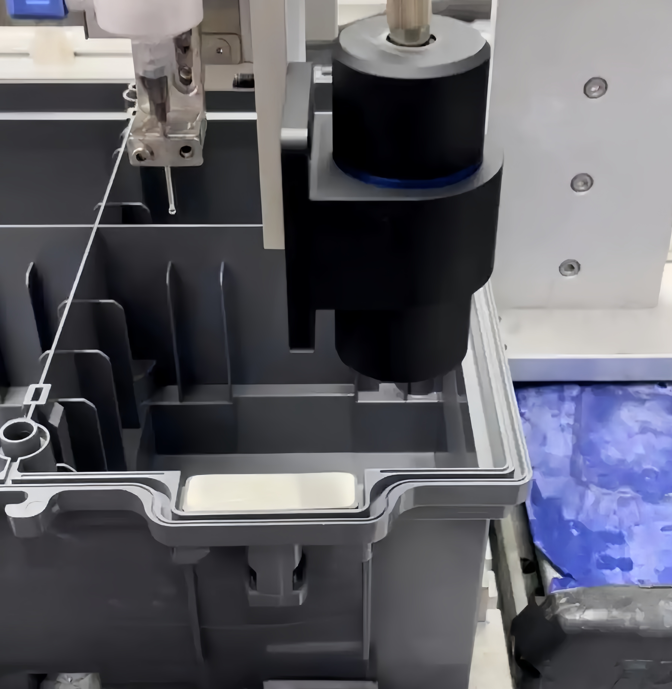
创新解决方案:LTC4000F光谱共焦传感器技术优势
基于LTC4000F系列光谱共焦位移传感器(参数详见表1),构建高鲁棒性涂胶检测系统,其核心优势如下:
技术特性 | LTC4000F参数 | 应用适配性 |
---|
超小光斑(Φ16μm) | 聚焦光斑直径16μm(中心量程) | 穿透5mm深槽,避免侧壁干扰 |
高重复精度(0.1μm) | 静态重复性RMS 0.1μm | 胶厚波动检测灵敏度提升30倍 |
抗倾角测量(±21°) | 允许最大入射角±21° | 适应拐弯处胶体曲面反射 |
高速采样(21kHz) | 控制器LT-CCH支持21kHz采样 | 匹配200mm/s涂胶速度无拖影 |
温漂抑制(<0.03% F.S/°C) | 温度稳定性0.12μm/°C | 车间温漂环境下长期精度保持 |
表1:LTC4000F关键参数与工艺适配性分析

系统设计与实施细节
1. 多光斑协同扫描策略
2. 抗干扰信号处理
3. 闭环控制集成
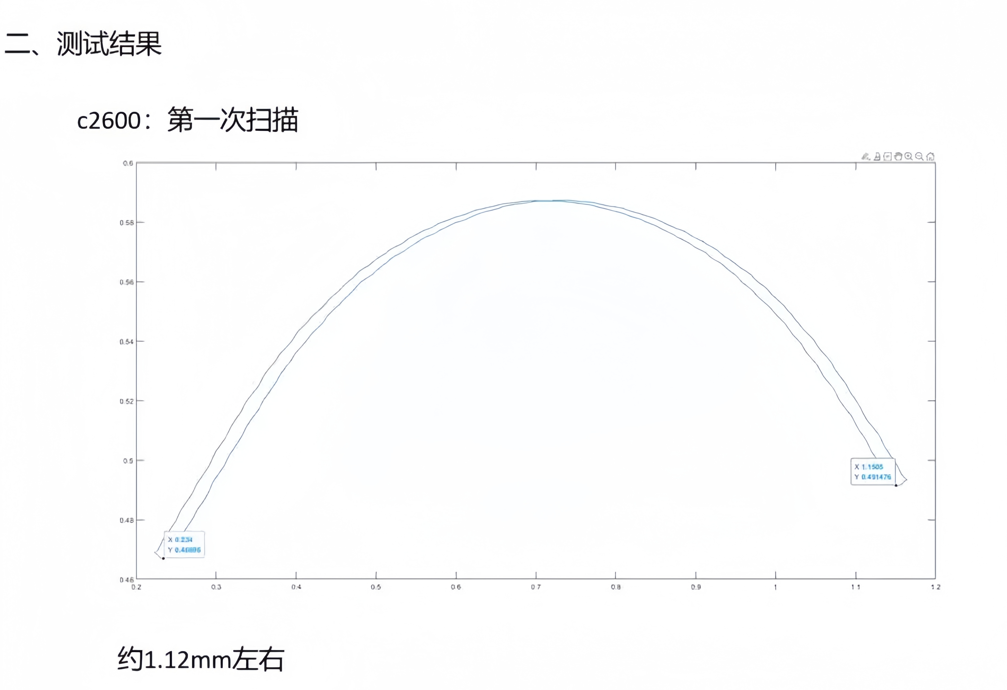
实测效能与经济效益
缺陷检出率:断胶、溢胶等缺陷检出率从82%提升至99.97%(基于10万组样本统计),漏检率低于50ppm。
工艺优化:胶体填充一致性标准差从±25μm降至±3.5μm,电池气密性测试通过率提高22%。
成本节约:年减少因涂胶不良导致的返修成本超500万元,设备投资回收周期<8个月。
行业启示
LTC4000F系列通过**“亚微米精度+深窄空间穿透+环境抗扰”**三重技术突破,解决了锂电涂胶检测的行业性难题。其模块化设计(支持高温200°C定制版本)更可拓展至注塑件毛刺检测、燃料电池双极板密封等场景,为新能源装备智能化升级提供标准化测量范式。
图例说明