[摘要]基于光谱共焦测量技术搭建了叶尖间隙模拟测试平台,将模拟叶盘安装在气浮主轴上,并应用光谱共焦位移传感器实现了叶尖端面的位移变化量的测量,以表征叶尖间隙的变化,分别模拟了叶尖间隙的单次测量和连续测量过程。实验结果表明,应用光谱共焦位移传感器可以完成发动机转子叶尖间隙的测量,而且能够达到很高的测量效率和精度,可以应用于实际的测量现场。
[关键词]叶尖间隙;非接触;光谱共焦;测量
引言
随着科学技术的长足进步,世界航空工业进入了全新的发展时代。在航空领域中,发动机是推进系统的重要组成部分,为飞机提供持续飞行的拉力或推力。作为飞机的核心部件,发动机对于飞行的安全性、可靠性和经济性等都有着重要影响。当前,航空推进系统日益向着高转速、高效率、高推重比、高可靠性和高涡轮前温度的方向发展,这就对发动机的整体性能提出了更高要求,迫切需要压气机、涡轮等关键部件具备更高的工作效率和更宽的稳定工作范围。而要达到这一目标,就需要着力加强在发动机性能测试方面的研究工作。
一般说来,航空发动机是一种高速旋转的热力机械,能够将燃料的化学能转化为飞机的动能,其各级转子主要由叶片、轮盘和转轴等部分组成。在发动机的运行过程中,压气机和涡轮中的转子以很高的转速做定轴回转运动,其中,各级转子叶片的顶端(叶尖)与机匣内壁之间的径向间距被称为叶尖间隙(Tip Clearance)。叶尖间隙是关系到发动机性能的重要参数之一,间隙过大,会使叶尖泄露增大,导致发动机效率下降,甚至造成发动机喘振;而间隙过小,则有可能导致叶片顶端与机匣内壁之间发生碰撞和摩擦,影响发动机的安全运转,甚至造成发动机损坏,给飞行带来巨大的安全隐患。
因此,采取必要的测试手段对发动机的转子叶尖间隙进行实时有效测量,从而掌握叶尖间隙的变化规律,对于监测发动机的工作状态,进而实现发动机整个运行过程的直接监测和故障诊断,都具有着重要而深远的意义。目前,叶尖间隙的测量方法主要有放电探针测量法、电涡流测量法和电容测量法等。放电探针法适用于导电材质的叶片,而且只能测量旋转叶片的最小叶尖间隙;电涡流法要求叶片材质具有导电性,并且叶尖端面要具有一定的厚度;电容法的频率响应性能较差,而且要求叶片材料必须是铁性材料,应用范围受到一定限制。可见,传统的测量方法存在着诸多局限性,不利于叶尖间隙测量任务的完成。
随着光学、电子学和传感技术等学科的发展与进步,许多光电传感器和测量方法被引入到航空领域中,成功地解决了许多传统测量技术难以或者无法解决的问题。其中,光谱共焦位移传感器是近年来新出现的一种非接触式的高精度光电位移传感器,基于光谱色散原理,能够将位移信息编码到波长信息中,再通过光谱分析技术得出被测位移,系统的分辨率可以达到微纳米量级,响应频率能够达到千赫兹量级。与传统的激光三角反射式位移传感器相比,光谱共焦位移传感器对被测表面的要求更低,允许被测表面有较大的倾斜角度。此外,它还具有精度高、绝对式测量、便于小型化以及对杂散光有较强的鲁棒性等特点,应用前景十分广阔。国内的马小军等提出了基于光谱共焦传感器的金属薄膜厚度测量技术,利用相向对顶安装的传感器组、精密位移平台等实现了对厚度为10~100μm的自支撑金属薄膜的厚度及厚度分布的精确测量。朱万彬等研究了将光谱共焦位移传感器用于测量透明材料平板厚度的可行性,并对其产生的误差进行了详细分析,给出了相应的补偿方法。陈挺等在论述光谱共焦技术原理的基础上,列举了光谱共焦传感器在几何量计量测试中的典型应用,探讨了共焦技术在未来精密测量领域中的进一步应用。
为了实现航空发动机转子叶尖间隙的实时精确测量,本文提出了一种基于光谱共焦技术的叶尖间隙测量方法。搭建了叶尖间隙模拟测试系统,将模拟叶盘零件安装在气浮主轴上,以模拟发动机转子,并将光谱共焦位移传感器固定在刚性支架上,通过支架的调整使传感器处于正确的工作位置。在实验过程中,首先进行单次测试,完成了单个叶片顶端位移变化量的测量;然后进行连续测试,旋转模拟叶盘,完成了该叶盘周向上36个叶片顶端位移变化量的连续测量,从而模拟了在发动机环境中的实际应用效果。实验结果表明,本文选用的光谱共焦位移传感器具有很高的测量精度和响应频率,并且体积小、便于安装,能够满足发动机叶尖间隙的测量需求。
1光谱共焦位移传感器的基本原理
光谱共焦测量技术最早由Molesini等人提出,并成功应用于表面轮廓仪。随后,许多科研人员都对基于光谱共焦原理的测量技术开展了深入研究,并在宏观和微观测量领域衍生出了许多应用实例。目前,国外的工业级光谱共焦位移传感器的测量精度已达到亚微米级,响应频率已达到几千赫兹。
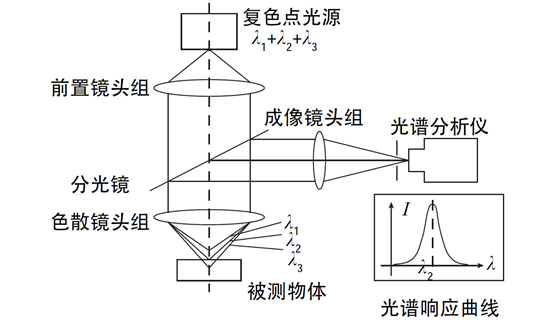
图1光谱共焦位移传感器的工作原理
光谱共焦位移传感器是在共焦显微镜的基础上发展起来的,其原理类似于共焦显微镜,但又有所不同。如图1所示,传感器主要由探头和光谱分析仪两部分组成,二者可通过光纤连接进行信号传输。其中,探头主要由光源和光学透镜组等构成。光源采用宽光谱的复色点光源(呈白光),其出射光束经过前置透镜组后变为多色平行光;然后通过后面的色散透镜组进行光谱分光,形成一系列波长不同的单色光,并将其进行同轴聚焦。由此产生光谱色散,将不同波长的光的焦点分散在光轴上的不同位置,从而在有效量程范围内形成了一系列焦点,每个焦点处的单色光波长都对应一个轴向位置,由此将位移信息转换为波长信息。最后,聚焦于被测物体表面的单色光被反射回来,通过分光镜进入成像透镜组并最终成像在针孔像面上。在此过程中,对应被测表面位置并满足共焦条件的单色光将进入针孔到达光谱分析仪,以进行后续处理;而离焦反射的其它光谱则被针孔遮挡,不能进入光谱分析仪。
进入针孔的单色光到达光谱分析仪后,可以根据光信号确定出此单色光的波长。由于每个波长都对应着一个距离值,因而根据波长就可以推算出相应的位移量,实现位移的精确分辨。光谱分析仪得到的光谱响应曲线如图2所示,横坐标表示波长λ,纵坐标表示对比度I。对于得到的光谱响应曲线,其峰值波长在555nm处,如果被测物体发生微小位移,那么在光谱分析仪上就可以得到另外一条光谱响应曲线,从而获得另一个峰值,这两个峰值之差所代表的位移可以根据色散和波长的关系得出。
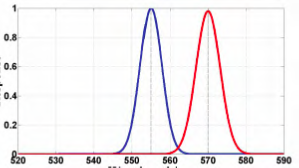
图2光谱响应曲线(长波/nm)
正是基于这种独特原理,使得光谱共焦位移传感器在位移测量上能够达到很高的分辨率和精度。对于单层和多层的透明物体,除了能准确测量该物体位移之外,还可以对其厚度进行单方向测量。如在测量薄玻璃片时,其前后表面都会反射特定波长的光,在光谱分析仪上能够获得具有两个峰值的光谱曲线,通过这两个峰值就可以推算出玻璃的厚度,这在检测一些很薄的物体时非常有效,如检测玻璃纸的厚度等。如果将光谱共焦位移传感器配置在二维扫描装置上,还可以用于测量物体的表面形貌,而普通的共焦显微镜则需要三维扫描装置才能够实现物体形貌的测量。
2叶尖间隙模拟测试系统
由于压气机的工作温度不是很高,而且光学环境较好,因此特别适合采用光电传感器对叶尖间隙进行测量。在测量过程中,将传感器固定在静子机匣的内壁上,通过传感器可以获得叶尖与传感器之间径向距离d1,再与传感器到机匣内壁之间的距离d2相加,即可得到待测的叶尖间隙d的值,即d=d1+d2,如图3所示。而在实际使用过程中,由于传感器与静子机匣的相对位置固定,因而d2的数值不会发生变化,因此叶尖间隙的变化量可以通过d1来表征。
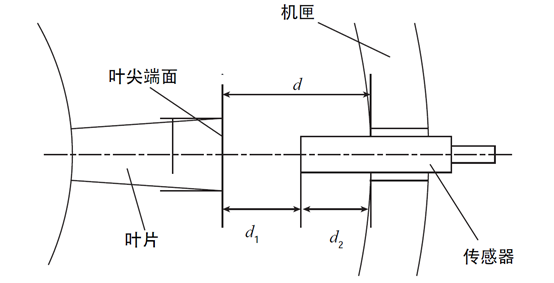
图3叶尖间隙的计算示意图
为模拟实际的测量现场,本文搭建了叶尖间隙模拟测试系统,如图4所示,主要包括光谱共焦位移传感器、刚性支架、模拟叶盘、气浮主轴、减振底座以及工控机等。首先,将刚性支架和气浮主轴固定在减振底座上,并调整它们之间的相互位置。其次,应用工装夹具将光谱共焦传感器安装在刚性支架上,由于该传感器采用侧向出光方式,其位移测量的方向与自身轴线垂直,因此应通过微调机构调整其空间方位,使传感器的轴线与气浮主轴的轴线平行。然后,将模拟叶盘安装在气浮主轴上,由于发动机转子的转速很高,因而整个气浮主轴系统在使用前需要经过动平衡调节,以使其在高速状态下稳定运转,不发生危险。最后,调整光谱共焦传感器的轴向位置,使其测量光束能够照射到模拟叶盘零件的叶尖上,在叶尖端面上形成测量点,并处于量程范围内。另外,在气浮主轴上还安装有转速同步器,以用于监测主轴的转速和转角位置,并将其作为光谱共焦传感器的同步信号。
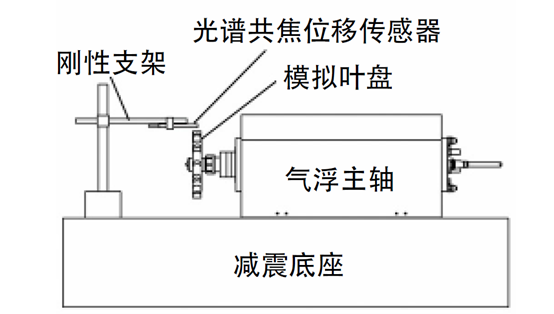
图4叶尖间隙模拟测试系统的结构简图
在间隙传感器方面,如图5所示,主要由控制器和探头组成,它们由一根光纤连接,控制器通过光纤向探头提供光源,探头再通过光纤将光信号传输到控制器中进行光谱分析。该测量系统可以对漫反射或镜面反射物体进行高精度的位移测量,还可以对透明物体的厚度进行测量。
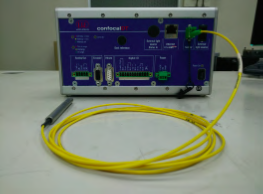
图5光谱共焦测量系统
控制器具有优异的信噪比,能够满足高精度测量的需求,测量速率可以达到10kHz,并且具有快速表面补光功能,可以通过控制曝光时间来达到较高的信号稳定性。数据输出可以通过Ethernet、EtherCAT、RS422或模拟量输出来实现。探头为光谱共焦式复合探头,采用无磨损透镜系统设计,可以进行径向测量,还能用于有防爆要求的工作领域与真空环境。该探头应用梯度指数透镜与光纤的复合技术,具有更大的数值孔径,因此可有效增大安全距离并加大安装倾斜角度。
3 实验验证
本文选取的光谱共焦位移传感器具有较小的尺寸结构和较高的响应频率,非常适合于航空发动机内狭小而恶劣的工作环境,因此在叶尖间隙测量方面具有很大的应用潜力。为了验证该型传感器在发动机叶尖间隙测量中的应用效果,本文在所搭建的叶尖间隙模拟测试系统上进行了单次和连续的测试实验,完成了传感器应用效果的综合验证。
3.1 单次测试
在本文搭建的模拟测试系统中,没有设计发动机机匣的模拟零件,因此间隙传感器通过刚性支架来模拟在机匣内壁上的安装状态。在叶片划过测量区域的过程中,传感器的输出为叶尖端面与传感器之间位移值,即d1。由于叶尖端面的厚度很小,因而叶尖间隙值可通过单个叶片划过时传感器的输出量的平均值来表征,实验现场如图6所示。
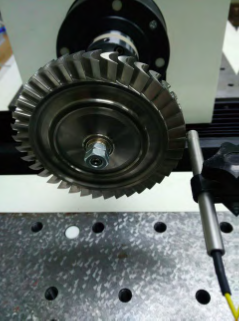
图6单次测量实验现场
通过变频器控制气浮主轴的转速,使其以缓慢速度带动模拟叶盘匀速转动。当叶片顶端进入光谱共焦传感器的测量范围内时,触发传感器开始数据采集;当叶片顶端转出传感器的测量范围时,传感器停止数据采集。在叶片顶端划过传感器测量范围的过程中,传感器采集到的测量数据如图7所示。
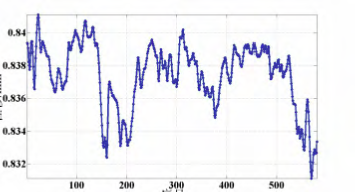
图7单个叶尖间隙的测量数据
从图7中可以看出,传感器在被测叶片顶端划过的过程中共采集到580个数据点,被测叶片顶端的位移变化量的范围为0.8311~0.8411mm,变化量的均值为0.8374mm,方差为0.0020mm。实验结果表明,应用光谱共焦位移传感器能够满足单个叶片叶尖间隙的测量,可以达到较高的测量精度。
3.2 连续测试
通过控制变频器调节气浮主轴的转速,使其带动模拟叶盘以1000r/min的速度回转。应用光谱共焦位移传感器进行模拟叶盘周向上的36个叶片的叶片顶端位移变化量的数据采集,并以平均值作为每个叶片最终的叶尖间隙值,动态测试的实验现场如图8所示。
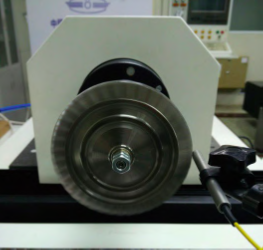
图8连续测量实验现场
计算得到的模拟叶盘周向上的36个叶片的叶尖间隙的实验数据如表1所示,同时为了便于观察叶尖间隙的变化趋势,将这些数据显示在同一坐标系中,如图9所示。可以看出,在本文所搭建的叶尖间隙模拟测试系统中,应用光谱共焦位移传感器可以完成对模拟叶盘全部叶片的叶尖间隙的测量。传感器能够达到很高的测量精度和响应频率。从表1和图9中可以看出,该模拟叶盘上36个叶片的叶尖间隙值的变化范围为0.7137~0.8438mm,并且呈现为近似正弦曲线的形状,这主要是由于在将模拟叶盘安装在气浮主轴上时,存在一定的偏心误差造成的。由此可以看出,发动机转子不同轴会对叶尖间隙造成影响,因而在发动机的装配过程中,应控制转子系统的不同轴误差在允许的范围内。
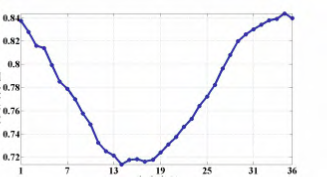
图9连线测量的实验数据(叶片序号)
表136个叶片的叶尖间隙的实验数据
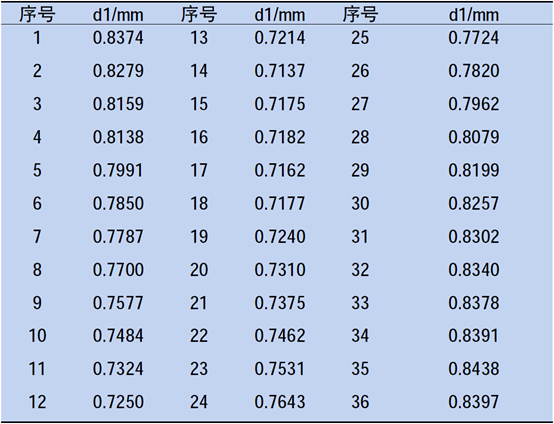
4 结论
针对航空发动机转子叶尖间隙的测量问题,本文探索了光谱共焦位移传感器在此方面的应用效果。光谱共焦位移传感器基于光谱色散原理,探头体积小、安装方便,并且能够达到很高的测量精度和响应频率,能够满足叶尖间隙的测量需求。本文搭建了叶尖间隙模拟测试系统,应用光谱共焦位移传感器对安装在气浮主轴上的模拟叶盘进行测量,采集叶片顶端位移变化量的数据。在实验验证过程中,本文既通过单次测量完成了单个叶片逐个检测,又通过连续测量完成了旋转状态下的每个叶片叶尖间隙的数据采集,系统具有良好的应用性能。实验结果表明,光谱共焦位移传感器可以用于发动机转子叶尖间隙的测量,从而为我国航空发动机技术的进步提供了一项测试技术支持。