摘要:为了提高加工检测效率,实现尺寸形位公差与微观轮廓的同平台测量,提出一种基于光谱共焦位移传感器在现场坐标测量平台上集成表面粗糙度测量的方法。搭建实验测量系统且在Lab VIEW平台上开发系统的硬件通讯控制模块,并配套了高斯轮廓滤波处理及表面粗糙度的评价环境,建立了非接触的表面粗糙度测量能力。对标准台阶、表面粗糙度标准样块和曲面轮廓样品进行了测量,实验结果表明:该测量系统具有较高的测量精度和重复性,粗糙度参数Ra的测量重复性为0.0026μm,在优化零件检测流程和提高整体检测效率等方面具有一定的应用前景。
关键词:计量学;表面粗糙度;光谱共焦;测量控制;在线集成;轮廓滤波器
1 引言
表面粗糙度是描述表面微观轮廓基本特点,评价产品表面质量最常用的参数之一。在机械加工、薄膜制备、微纳机电系统、光学精密加工等领域中,表面粗糙度是评价产品性能的重要指标之一。表面粗糙度与加工零部件的摩擦磨损性能、耐腐蚀性能、结合密封性、抗疲劳能力等存在必然联系,进而对零件和制造设备的稳定性和可靠性产生重要影响。表面粗糙度也是开展功能结构部件微观表面形貌评价与表征的重要参数。
然而,目前在表面粗糙度和微观轮廓的测量工业应用中,常见使用的是宝石触针接触式轮廓仪和扫描白光干涉轮廓仪等精密设备。这两种精密仪器对使用环境和条件要求较为严格,不适合用于要求高检测效率和在线测量的工业现场。
三坐标测量机是加工现场最常用的高精度产品尺寸及形位公差检测设备,其具有通用性强,精确可靠等优点。本文面向一种特殊材料异型结构零件内曲面的表面粗糙度测量要求,提出一种基于高精度光谱共焦位移传感技术的表面粗糙度集成在线测量方法,利用工业现场常用的三坐标测量机平台执行轮廓扫描,并记录测量扫描位置实时空间横坐标,根据空间坐标关系,将测量扫描区域的微观高度信息和扫描采样点组织映射为微观轮廓,经高斯滤波处理和评价从而得到测量对象的表面粗糙度信息。
2 测量系统及原理
2.1 测量系统
在线集成表面粗糙度测量系统是以一台三坐标测量机(CMM)为平台构建,其结构由光学探头、白光光源、微型光谱仪、光纤、测量工装、上位机控制平台等部分组成,见图1。其中,以光学探头、白光光源、微型光谱仪、光纤等为主要元件组成光谱共焦位移传感系统,测量量程300μm,横向分辨率为4.5μm,纵向位移测量精度达nm级,较好地满足表面粗糙度测量对光探针尺寸和精度的要求。坐标测量平台利用其高精度和稳定的三维空间运动定位能力以及方便在线部署的特点,作为表面粗糙度测量的扫描运动执行器。
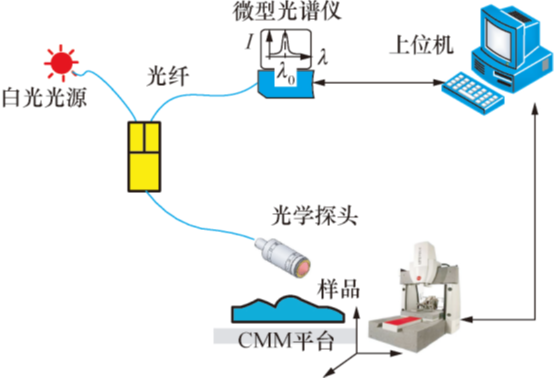
图1测量系统结构图
根据系统结构特点和坐标测量机测量臂末端接口形式,将光学探头通过转接紧固件可靠固定在测量臂末端,如图2所示。
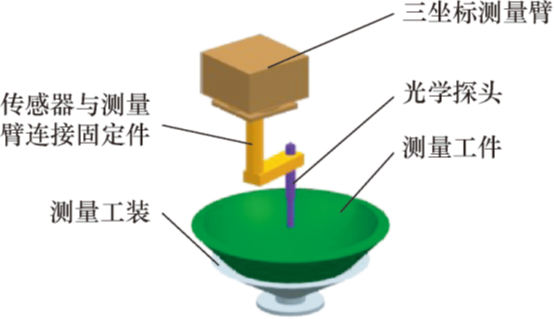
图2安装示意图
2. 2 测量原理和流程
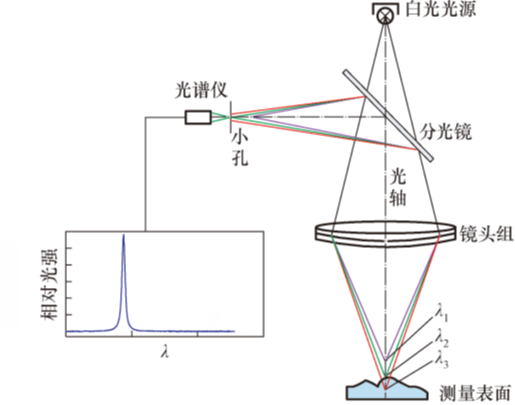
图3光谱共焦位移传感原理图
通过特殊光学设计形成的透镜组将白光光源发出的多色平行光进行光谱分光,形成一系列波长不同的单色光,同时再将其同轴聚焦,由此在有效量程范围内形成了一个焦点组,每一个焦点的单色光波长都对应着一个轴向位置。测量时通过光谱仪分析光谱峰值结合峰值提取算法从而确定被测点的高度位置信息。
表面粗糙度测量方法具体流程如下:
(1)待测工件定位。将待测工件平稳置于坐标测量机测量平台上,调用标准红宝石测针测量其空间位置和姿态,为按测量工艺要求确定测量位置提供数据。
(2)轮廓扫描。测量机测量臂更换挂载光谱共焦传感器的光学探头,驱动探头运动至工件测量位置,调整光源光强、光谱仪曝光时间和采集频率等参数以保证传感器处于较好的工作状态,编辑扫描步距、速度等运动参数后启动轮廓扫描测量,并在上位机上同步记录扫描过程中的横向坐标和传感器高度信息,映射成为测量区域的二维微观轮廓。
(3)表面粗糙度计算与评价。将扫描获取的二维微观轮廓数据输入到轮廓处理算法内进行计算,按照有关国际标准选择合适的截止波长,按高斯轮廓滤波方法对原始轮廓进行滤波处理,得到其表面粗糙度轮廓,并计算出粗糙度轮廓的评价中线,再按照表面粗糙度的相关评价指标的计算方法得出测量结果,最后得到被测工件的表面粗糙度信息。
3 硬件控制与轮廓处理环境的建立
3. 1 测量系统硬件控制架构
对工件微观轮廓的扫描和表面粗糙度测量,需在同一平台上协调控制扫描执行器和位移传感器。
基于USB和Ethernet通讯接口和协议,在上位机LabVIEW开发环境下进行了测头传感器和运动机构的通讯、控制、调节和数据流传输等功能的二次开发,形成了较为完善的测量系统硬件通讯控制架构,主体系统控制结构如图4所示。
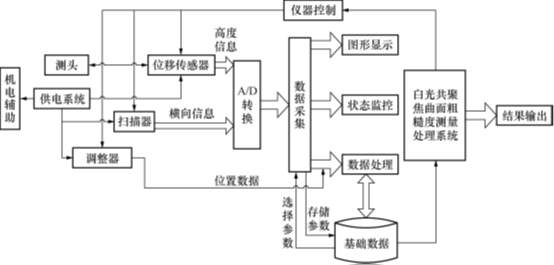
图4系统控制结构图
为了方便使用和测量,为控制系统开发了人机交互较为便捷的界面窗口,见图5,可方便的调控传感器相关参数指标,并预览扫描过程中的轮廓信息。还可以预设和编辑扫描运动策略,调整存储数据的名称等功能,并额外的增加了光谱信号展示、集成轮廓滤波与评价方法等功能,可以实现扫描测量后及时的数据输出。
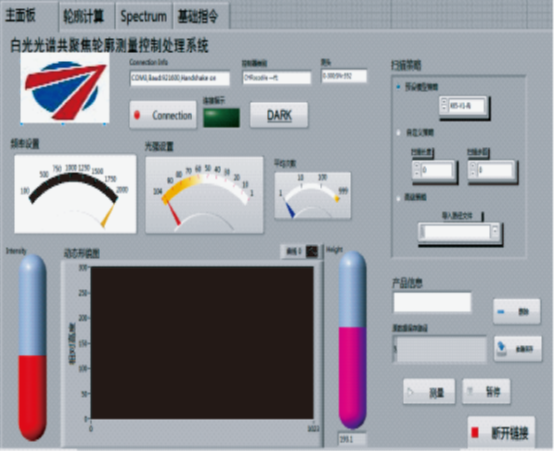
图5表面粗糙度测量系统控制前面板
3. 2 高斯轮廓处理方法
表面轮廓示意图如图6所示,传感器除了采集表面粗糙度信息之外,还将采集波纹度,几何形状等信息。轮廓滤波处理是指将轮廓信息分为不同频率成分。
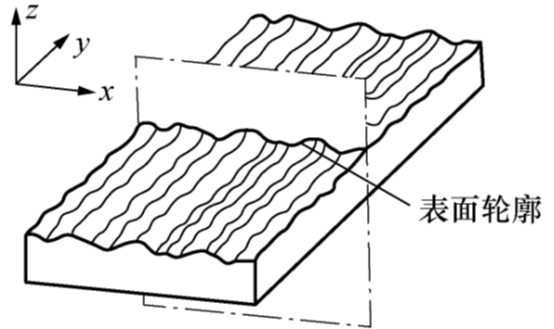
图6表面轮廓示意图
在轮廓处理算法中增加了整体轮廓预览、波纹度分析和数据整体等功能模块,其算法设计流程如图7所示,图7中的相关参数在GB/T3505中已作了明确定义。
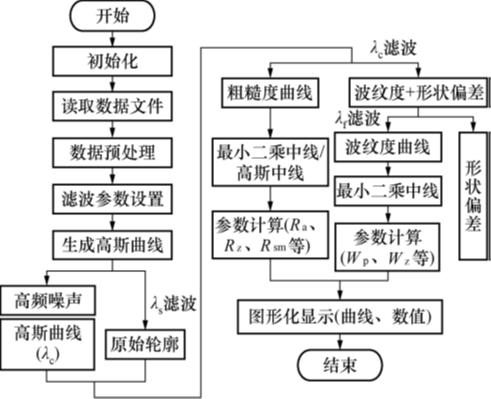
图7轮廓处理方法流程
利用LabVIEW与Matlab的混合编程模块,将高斯轮廓滤波及评价方法集成到了LabVIEW程序面板中,使用时调整滤波参数可及时调用滤波和评价算法实现测量数据的实时处理。
4 实验
为验证表面粗糙度测量系统测量的有效性,对标准台阶样品、标准表面粗糙度样块测试实验和某异形车削零件曲面轮廓表面粗糙度的测量实验。
4. 1 标准台阶测试实验
测试所用的标准样品上刻有两个测试台阶位置,其标称高度分别为9.3μm和9.4μm。利用搭建的测量系统沿台阶垂直方向对该样板进行扫描,对测量采集的数据轮廓进行校平、最小二乘拟合等处理,计算得两处台阶位置高度差分别为9.27μm、9.36μm,台阶轮廓如图8所示。
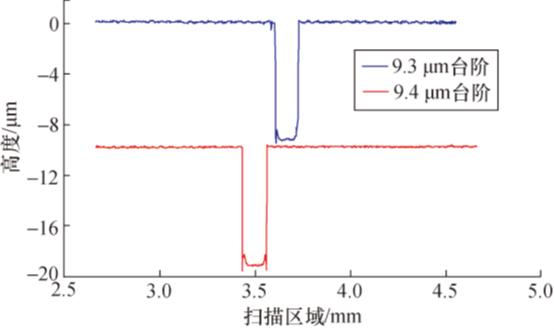
图8标准台阶的扫描轮廓
4.2 表面粗糙度标准样块测试实验
测试选用的为三角波纹理表面粗糙度标准样块,附DKD检定证书,其表面粗糙度算术平均偏差Ra的标定值为0.37μm。采用构建的集成表面粗糙度测量系统对标准样品进行测量验证测试。在标准样块刻线处选取3个不同测试位置,每个测试位置重复测量3次,见图9。
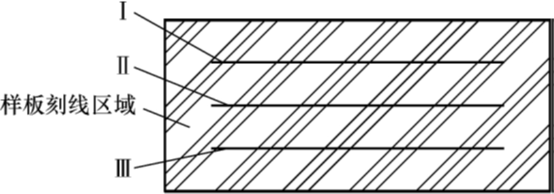
图9测量位置示意图
利用高斯滤波方法对原始轮廓数据进行表面粗糙轮廓滤波处理,并基于最小二乘中线分析计算其表面粗糙度算术评价偏差Ra值
轮廓计算处理过程中,位置Ⅱ的原始轮廓和滤波处理后的表面粗糙度轮廓如图10所示。
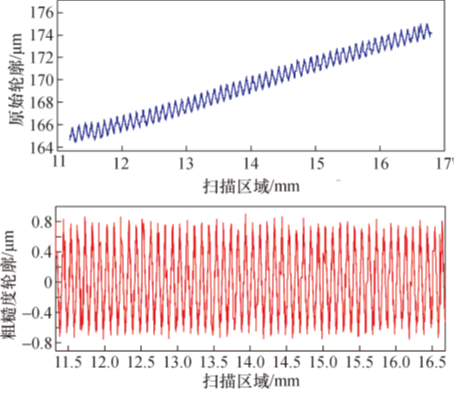
图10位置Ⅱ的原始轮廓和表面粗糙度轮廓
4.3 曲面轮廓测量样品测量实验
如图2所示的工件的内球曲面为其工作面,设计球径为180mm,采用车削加工成型,其加工和检测工艺上要求在其内球曲面不同的角度位置上检测型面表面粗糙度情况。在零件内球曲面轮廓的回转母线上回避顶点标记3段不同角度的测量位置,利用表面粗糙度测量,图11所示是位置Ⅱ的原始轮廓和滤波处理后的表面粗糙度轮廓。从图11可以看出,测量结果较稳定、可靠。
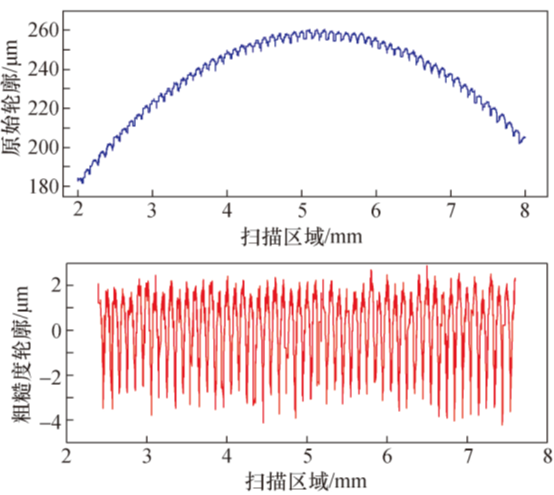
图11位置Ⅱ的原始轮廓与表面粗糙度轮廓
5 结论
本文面向一种特殊材料异型结构零件内曲面的表面粗糙度集成在线测量的要求,提出一种在坐标测量平台上集成光谱共焦传感器的方法,设计构建的测量系统,面向表面粗糙度测量的全流程建立了硬件控制与轮廓处理环境,进行了多项测量实验。实验结果表明:该测量系统具有较高的测量精度和重复性,粗糙度参数Ra的测量重复性为0.0026μm,通过优化零件检测过程,整体上缩短零件近30%的检测时间,可用于零件生产加工现场对表面粗糙度进行在线测量。